3D Design, Visualization and Prototyping. Part 4: Automotive Interiors
- ianmitchell1967
- Feb 19, 2024
- 5 min read
By Mitch
19th February, 2024

In Part 2 of this series, we looked at how 3D Design, Visualization and Prototyping can aid in the production of automotive lighting. This time though in Part 4, we're moving from the outside aesthetics and functionality of the lights on a vehicle to the inside and the interior fitments.
As we've said before, the look of a vehicle is probably the first thing that attracts you to it. Therefore, the exterior design is a crucial part in getting the customer to take that all important step to sitting in the driver's seat and getting a feel for the interior.
The interior not only needs to look stylish but also needs to be comfortable, safe and functional. Let's then take a look at those key aspects and see what's required to fulfill the design brief.
Style
In the world of automobiles and automotive design, style is usually at the forefront of both the designer's and user's mind. In the housing market for instance, first impressions of a property are what's known as "kerb appeal". If we then apply that to vehicles, you could almost say that it's "at the kerb appeal" that might draw you to it. That may be a weak analogy but hopefully you get the point!
The thing is though that we all look for something that, well, looks nice. So, in the same way that you might look for smooth and sleek lines on the exterior of a vehicle, you'd probably expect to see the same carried through to the interior.
Things like hard corners and sharp edges aren't desirable and in essence the interior fitments should only serve as a housing to the hidden wiring or control panels. 3D printed parts of a vehicle's interior are therefore mainly limited to the fascia's and casing which line it. We will though discuss later on the advances which are expanding the range of 3D printing in vehicle interiors. The overall design and style however should incorporate both 3D printed and production made parts seamlessly.
Comfort
This follows on from the style of the interior as we all of course need to feel comfortable when using our vehicle.
Comfort comes in different forms and this could be either the "fit" of the interior to you and your passengers or it can also be to how easy it is to access different areas and parts of the interior. For instance, there's no point having a handle which is impossible to reach or a cup holder that doesn't securely hold your drink.
Designer's need to take into account these aspects of the driving experience as well as including all the usual operational switches, dials and controls of the vehicle.
This then leads us nicely on to the functionality of the vehicle's interior.
Functionality
Of course, we can look at both style and comfort as being the "draw" to buying a vehicle, but neither of these are any good if the normal operations of the vehicle are in any way impeded. You could say that there's no style without substance.
As we've referred to previously, a vehicle's driver and passengers need to be able to use the functional parts of the vehicle with ease. Therefore, the fascias and housing of any controls for the doors, windows, aircon, lighting etc. need to be easily accessible while maintaining a discreet presence. In other words, controls should be obvious and available without being ostentatious and unnecessarily labelled. If you're old enough to remember the 1960s Batman TV show then you know what I mean!
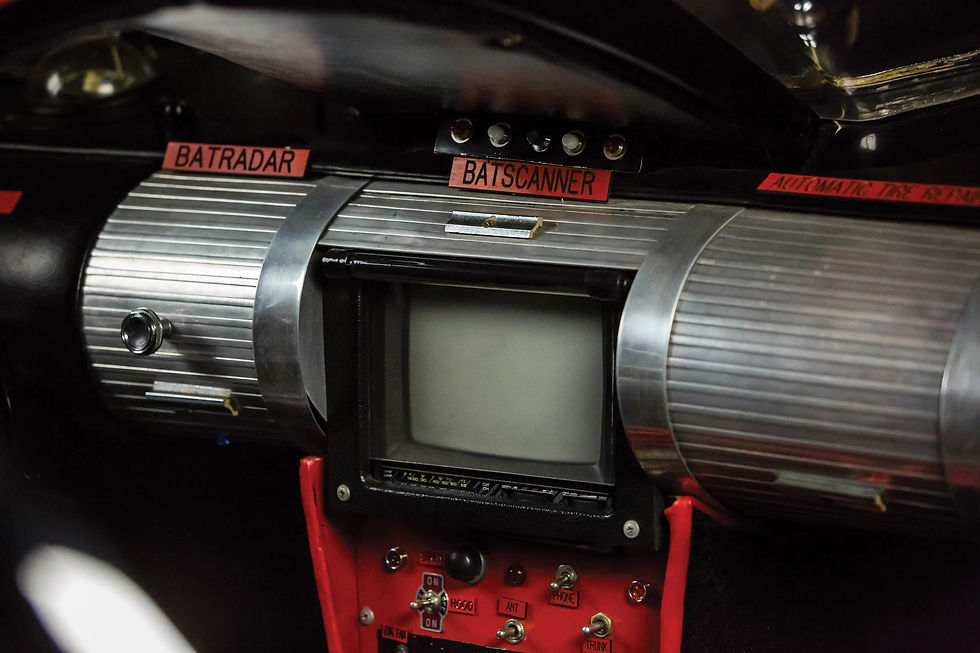
Safety
Being able to access all the controls and comfort aspects of a vehicle needs to be done in a safe way. Not only then should lines be smooth with no sharp edges or corners, but covers and access panels should be secure while also being easy enough to remove.
Certain panels within a vehicle's interior will only need to be removed if there's a problem with the vehicle. For instance, if you need to change a fuse or bulb or to add wiring for a sound system or alarm.
There are though covers for switches that may be used regularly and of course door and grab handles need to be secure and smooth so as not to cause injury. Everything therefore needs to be manufactured to the highest standard to ensure it fits together perfectly and leaves no margin for unnecessary accidents.
So, where then does 3D design, visualization and prototyping fit in making automotive interiors to meet all the specifications we've discussed? Again, let's take a look at each aspect individually.
3D Design

3D design, as we know, is the best way to bring your ideas to fruition and this is no different when it comes to automotive interiors.
The first stage of vehicle design is usually the exterior and is based on the type of vehicle you're looking for. If say it's a saloon car then the size is going to be an aspect along with speed, aerodynamics and streamlining. These are all things that are designed using CAD (Computer Aided Design) software, modelled, prototyped tested and then put into production. We'll be looking at this process relating to vehicle design in an upcoming article.
Once the exterior look and design of the vehicle has been finalized, it's time to make everything on the interior fit into place and be in keeping with the overall aesthetics and feel of the car. CAD will of course be used again but this time we're not looking at the streamlining or speed etc. of the vehicle but instead at the aspects we've covered above. The exterior shape of the vehicle will then determine the way the interior is designed.
3D Visualization
Once the CAD design has been made it's usual to visualize this using a computer render or simulated replica of each part.
The interior will be made up of many different shaped and sized parts and most of these will be unique and individually designed to fit the specific vehicle for which they are to be used. It's therefore important to include everything in the visual plan of the interior from the panelling and large area parts, right down to where the screws and nuts and bolts will go. If something is overlooked at this stage then the whole design may not work.
Once the design is visualized and complete then this will move us onto prototyping.
3D Prototyping
This is where 3D printing will come into play for the first time in this process. Later on of course, 3D printing can be used to actually produce the final product or interior part but at this stage we're looking at prototyping.
The CAD design can be transferred or converted into a 3D printable file and either an exact replica or a scaled model of the part can then be printed. This process is much quicker and more economical as a single part can be printed individually rather than having to do a larger production run.
The prototyped parts can then be assembled, studied and tested to ensure that they meet all requirements before putting the parts into final production.
Conclusion
3D printed automotive interiors are becoming much more commonplace as the technology advances and manufacturers realise the ease and cost effectiveness of the process. Obviously not everything that you would find in a vehicle interior is possible to 3D print but with the majority being predominantly plastic based, 3D printing is the obvious choice.

3D printed prototyping is of course a major part of what Politech as a business is all about and if you're commissioning professional prototypes for your product, then Politech is the place to come. Please see our contact details on the Homepage and we'll be happy to work with you.
Thanks for reading and please look out for our next article in this series and of course for more besides!
Comments